Slot die coating is a coating technique for the application of solution, slurry, or extruded thin film onto typically flat substrates such as glass, metal, paper, fabric or plastic foils.
![]() |
![]() |
Slot-die coating produces thin films via solution processing. The desired coating material is typically dissolved or suspended into a precursor solution or slurry (sometimes referred to as "ink") and delivered onto the surface of the substrate through a precise coating head known as a slot-die. The slot-die has a high aspect ratio outlet controlling the final delivery of the coating liquid onto the substrate. This results in the continuous production of a wide layer of coated material on the substrate, with adjustable width depending on the dimensions of the slot-die outlet. By closely controlling the rate of solution deposition and the relative speed of the substrate, slot-die coating affords thin material coatings with easily controllable thicknesses in the range of 10 nanometers to 100's of micrometers after evaporation of the precursor solvent.
Commonly cited benefits of the slot-die coating process include its pre-metered thickness control, non-contact coating mechanism, high material efficiency, scalability of coating areas and throughput speeds, and roll-to-roll compatibility. The process also allows for a wide working range of layer thickness and precursor solution properties such as material choice, viscosity, and solids content.
Film thickness control
Slot-die coating is a non-contact coating method, in which the slot-die is typically held over the substrate at a height several times higher than the target wet film thickness. The coating fluid transfers from the slot-die to the substrate via a fluid bridge that spans the air gap between the slot-die lips and substrate surface. This fluid bridge is commonly referred to as the coating meniscus or coating bead. The thickness of the resulting wet coated layer is controlled by tuning the ratio between the applied volumetric pump rate and areal coating rate. Unlike in self-metered coating methods such as blade- and bar coating, the slot-die does not influence the thickness of the wet coated layer via any form of destructive physical contact or scraping. The height of the slot-die therefore does not determine the thickness of the wet coated layer. The height of the slot-die is instead significant in determining the quality of the coated film, as it controls the distance that must be spanned by the meniscus to maintain a stable coating process.
Commonly cited benefits of the slot-die coating process include its pre-metered thickness control, non-contact coating mechanism, high material efficiency, scalability of coating areas and throughput speeds, and roll-to-roll compatibility. The process also allows for a wide working range of layer thickness and precursor solution properties such as material choice, viscosity, and solids content.
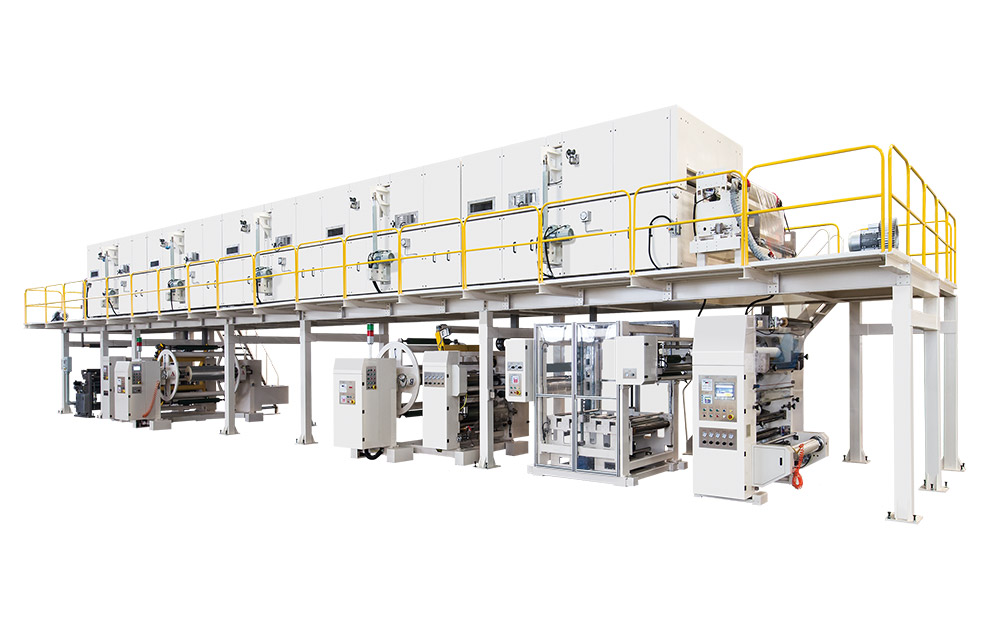
Slot-die coating is a non-contact coating method, in which the slot-die is typically held over the substrate at a height several times higher than the target wet film thickness. The coating fluid transfers from the slot-die to the substrate via a fluid bridge that spans the air gap between the slot-die lips and substrate surface. This fluid bridge is commonly referred to as the coating meniscus or coating bead. The thickness of the resulting wet coated layer is controlled by tuning the ratio between the applied volumetric pump rate and areal coating rate. Unlike in self-metered coating methods such as blade- and bar coating, the slot-die does not influence the thickness of the wet coated layer via any form of destructive physical contact or scraping. The height of the slot-die therefore does not determine the thickness of the wet coated layer. The height of the slot-die is instead significant in determining the quality of the coated film, as it controls the distance that must be spanned by the meniscus to maintain a stable coating process.
Industrial coating systems
Slot-die coating was originally developed for industrial use and remains primarily applied in production-scale settings. This is due to its potential for large-scale production of high-value thin films and coatings at a low operating cost via roll-to-roll and sheet-to-sheet line integration. Such roll-to-roll and sheet-to-sheet coating systems are similar in their intent for large-scale production, but are distinguished from each other by the physical rigidity of the substrates they handle. Roll-to-roll systems are designed to coat and handle flexible substrate rolls such as paper, fabric, plastic or metal foils. Conversely, sheet-to-sheet systems are designed to coat and handle rigid substrate sheets such as glass, metal, or plexiglass. Combinations of these systems such roll-to-sheet lines are also possible.
Slot-die coating was originally developed for industrial use and remains primarily applied in production-scale settings. This is due to its potential for large-scale production of high-value thin films and coatings at a low operating cost via roll-to-roll and sheet-to-sheet line integration. Such roll-to-roll and sheet-to-sheet coating systems are similar in their intent for large-scale production, but are distinguished from each other by the physical rigidity of the substrates they handle. Roll-to-roll systems are designed to coat and handle flexible substrate rolls such as paper, fabric, plastic or metal foils. Conversely, sheet-to-sheet systems are designed to coat and handle rigid substrate sheets such as glass, metal, or plexiglass. Combinations of these systems such roll-to-sheet lines are also possible.
Both industrial roll-to-roll and sheet-to-sheet systems typically feature slot-dies in the range of 300 to 1000 mm in coating width, though slot-dies up to 4000 mm wide have been reported. Commercial slot-die systems are claimed to operate at speeds up to several hundred square meters per minute, with roll-to-roll systems typically offering higher throughput due to decreased complexity of substrate handling.
Industrial applications
Slot-die coating was originally developed for the commercial production of photographic films and papers. In the past several decades, it has become a critical process in the production of adhesive films, flexible packaging, transdermal and oral pharmaceutical patches, LCD panels, multi-layer ceramic capacitors, lithium-ion batteries and more.

Slot-die coating was originally developed for the commercial production of photographic films and papers. In the past several decades, it has become a critical process in the production of adhesive films, flexible packaging, transdermal and oral pharmaceutical patches, LCD panels, multi-layer ceramic capacitors, lithium-ion batteries and more.

Research applications
With growing interest in the potential of nanomaterials and functional thin film devices, slot-die coating has become increasingly applied in the sphere of materials research. This is primarily attributed to the flexibility, predictability and high repeatability of the process, as well as its scalability and origin as a proven industrial technique. Slot-die coating has been most notably employed in research related to flexible, printed, and organic electroniscs, but remains relevant in any field where scalable thin film production is required.

With growing interest in the potential of nanomaterials and functional thin film devices, slot-die coating has become increasingly applied in the sphere of materials research. This is primarily attributed to the flexibility, predictability and high repeatability of the process, as well as its scalability and origin as a proven industrial technique. Slot-die coating has been most notably employed in research related to flexible, printed, and organic electroniscs, but remains relevant in any field where scalable thin film production is required.

Examples of research enabled by slot-die coating include:
- Thin film solar cells, to produce electron transport layers, hole transport layers, photoactive layers, and passivating layers
- Solid state and next-gen batteries, to produce electrodes, solid electrolytes, ion selective membraines, protective coatings, and interface modification coatings
- Fuel cells and water electrolysis, to produce electrolytes and electrode catalyst coatings
- Flexible touch-sensitive surfaces, to produce transparent conductive films
- OLED devices, to produce electron transport layers, hole transport layers, and electroactive layers.
- Printed diagnostics and molecular sensors, to produce active layers and ion selective membranes
- Microfluidics and lab-on-a-chip devices, to produce hydrophobic/hydrophilic surface coatings for enhanced liquid flow
- Water purification, to produce nanofiltration membranes
- Biobased and biodegradable packaging, to produce multilayer barrier foils from sustainable materials

Main contents cited from Wikipedia